The Problem
Moran Farms is a large agriculture and grain production leader in the Pine Lake area, farming over 6000 acres. Over the years, the farm’s bin storage capacity has grown to over 20+ bins, storing over 400,000 bushels. During harvest, the challenge of efficient grain storage and transportation has become evident when using portable grain augers and tractors. As production increased, Moran farms needed higher capacity grain augers with longer reaches, making them very large and difficult to move safely. Moving these large grain augers from one bin to another required two people to move them around safely and efficiently. During the busy harvest season, this was stressful because you had to do this quickly so the grain truck could get back to the field and unload the next combine. These large grain augers also take up a lot of space to operate and create potential safety hazards when unloading trucks at the end of a long day.
Another issue was that two people were needed to fill these large bins to ensure they were not overfilled and prevent grain from being spilled onto the ground. In addition, managing this inventory, once in the bins, became time-consuming, especially when it came to monitoring and controlling grain moisture content.
They needed to install a grain handling system that quickly unloaded grain trucks from the field and automatically augers grain to the desired bin location, eliminating the need for portable grain augers. Once in the bins, they needed an inventory management system and the ability to move the grain from one bin to another.
The Solution
Moran Farms knew that efficient grain handling was crucial for ensuring the quality and integrity of the grains, preventing spoilage, and facilitating the timely and cost-effective movement of the products from the field to the storage bins. The system starts with a flat-top truck scale where trucks drive onto the scale and unload the grain into a hopper where a 12″ Lambton Loop drag conveyor and 12″ Lambton Cannon Drag Conveyors move the grain into the selected bin location.
This grain-handling loop system is designed for one person to unload the truck and move the grain to the desired storage bins with the push of a button.
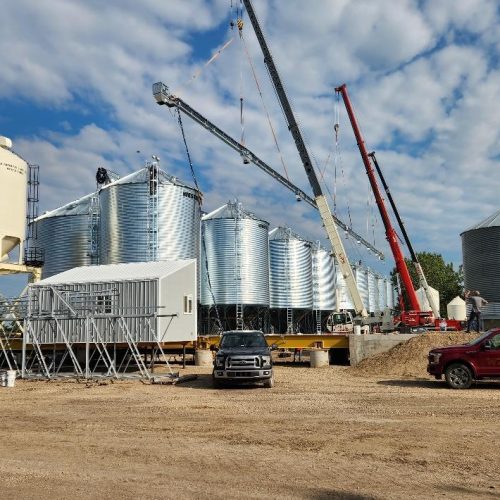
Each bin had level sensors installed. When the bin reached maximum capacity during the truck unloading operation, the system automatically switched to another bin, preventing the bin from overfilling and spilling grain onto the ground. The system is designed to handle 10,000 bushels per hour of grain, so unloading the truck and returning to the field happens quickly.
Once the grain is in the bins, OPI grain sensors measure the temperature and moisture of the stored grain. Natural grain conditioning increases the storage life of grain and minimizes grain spoilage and quality loss. The PLC program first mixes wet grain from one bin with dry grain from another bin to condition the grain naturally. Natural air in-bin drying is the highest quality and most energy-efficient process. If cooling is required, the PLC program will turn the aeration system on and off until acceptable temperature and moisture levels are met.
When it comes time to sell the grain to market, the conditioned grain is first confirmed to be market-ready by the grain management system. Then the farmer pushes a button on the PLC Panel Screen to transfer the grain from the storage bin to a 1000-bushel cone-bottom grain silo located above the weight scale to load trucks quickly. Trucks are loaded to correct axel weight and road allowance loads before heading to the grain elevator.
Services Provided
Moran Farms and their mechanical contractor, Skyway Grain Systems, selected Current Group to design and install an automated control system because of our experience automating grain management systems. They knew grain handling loops were complex systems that allow multiple scenarios to store and process grain within the storage facility. The project needed an agriculture automation integrator with PLC programming experience to connect the sensors and motors to the grain management system. The control system included motors, Levalert bin level sensors, electric distributor gates, and a programmable logic controller (PLC) to monitor and control the grain flow.
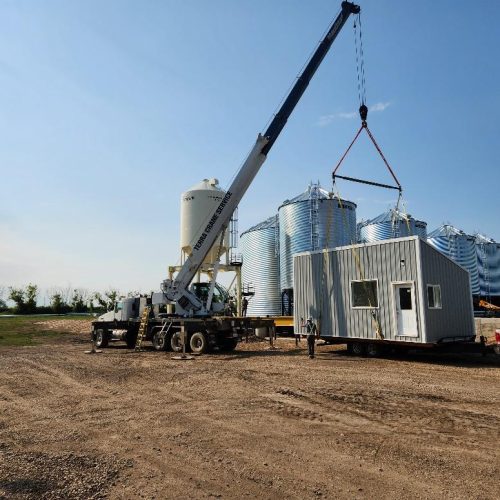
Current Group was also responsible for the building and installation of the scale shack, which doubled as the system’s control room. Besides the weight scale equipment, the building also included the PLC control panel, MCC control panel, and marshalling panel for all the end devices. Electric and control cables were installed between the motors, sensors, and scale shack. Finally, an LED lighting package was installed so the facility was safely lit for those late-night truck unloads.
A Caterpillar 300 kW diesel generator was installed to power the system because it was cheaper than connecting to utility power. The generator was easily started from the control room with a push of a button on the panel.
The term “loop system” refers to a continuous, circular flow of grains within the facility. This looping design can enhance efficiency by minimizing the need for backtracking and optimizing the overall grain-handling process.